Shipwire provides best practices for product configuration that help you deliver a complete brand experience, grow your business across markets and channels, and drive down overall logistics spend.
This support page will give you a better understanding of how your product catalog works, and how to use these best practices to your advantage in configuring individual products or cartons.
To learn more about how to optimize your product configuration for bulk shipping, read our Shipping in bulk guide.
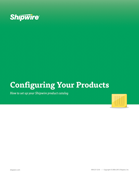
Download the Configuring Your Products guide
Our printable Configuring Your Products PDF guide will show you how to set up your product catalog. Learn the best practices and get a step-by-step guide for setting up units and cases.
Why proper product setup is important
Shipwire defines products in an optimal way which lets you manage both B2C (individual units) and B2B (wholesale cases) sales within the same product structure. Proper product setup also allows you take advantage of automated lot breaks and bulk optimization.
Using these best practices helps Shipwire understand how a product is packaged and how ‘like units’ are coming in (i.e. the product can be picked at the Base Product level, the Inner Pack level, the Master Case level, and for B2B orders, the Pallet level).
Each level of your product packaging must have a unique product ID (typically referred to as a SKU, or Stock Keeping Unit) before being sent to our warehouses. This will help Shipwire identify each individual product and/or the cases containing multiple instances of a product.
There are four types of SKUs – base products, inner packs, master cases, and pallets. We suggest following the Shipwire best practices for defining the relationship between these SKUs:
Base Products | A base product can be the individual unit of a particular product. |
Inner Packs | Inner Packs are cases containing a certain number of units. All the products inside Inner Packs must be of the same Base Product. If there is more than one type of SKU inside an Inner Pack then it should be defined as a kit. |
Master Cases | Master Cases are larger cases containing a certain number of Inner Packs. |
Pallets | Pallets contain stacked Master Cases placed on a wooden frame. |
The SKU relationship will work in the same way as when you open the pallet – the pallet will contain several master cases which contains multiple inner packs, and each inner pack contains several units.
Matching SKUs to the physical product label
The SKU names in your account have to match the SKUs on the physical label on your product. For example, if the SKU on your products is 123-ABC, the SKU for that product should also be 123-ABC when setting up your Shipwire product catalog. This helps us keep a unified product catalog structure and prevent errors when passing on orders to our warehouses.
Inner Packs vs. Kits
In some cases you will have a different combination of products using the same SKU as what is contained in the inner pack, but won’t want them to be sold individually. For example, a two-pack of bottles that cannot be broken down into two individual units. In Shipwire, these are defined as kits. Kits should have their own unique SKU and should be clearly marked KEEP AS KIT on the label.
Shipping a master case that is not a kit
If you are sending a case containing different SKUs (either units or smaller inner packs) and do not wish to keep it as a kit, it will be broken down when it is received by the warehouse and its contents will be inventoried. In this case you do not include KEEP AS KIT on the label. Labelling for this type of shipment has specific requirements.
See our label specifications for this type of case.
Using kits: When a contained SKU is already part of an existing SKU hierarchy
You may have a product (for example SKU A) that is already used in a set SKU relationship that is clearly defined. In some cases, you may need to include a separate case of product A that does not fit into this hierarchy. For example, you may have the following relationship set up:
Base Product | A |
Inner Pack | 6 x A |
Master Case | 24 x A (defined as 4 x inner pack) |
and may also need to inventory a case that contains 5 base products of A, which does not fit into the above relationship. If you don’t want this new case of 5 x A to be broken down into single units, then you must define it as a kit with a new SKU (for example, A-5PACK), and clearly mark KEEP AS KIT on the label. This will ensure that when an order for a single unit of A comes in, it will not be taken out of the new kit that only sells as a pack of 5.
FAQ
Q.How do I add products in my Shipwire account?
A.See our Adding and configuring products page.
Q.How do I add product in bulk via a spreadsheet?
A.See our Adding and configuring products page.
Q.Why are my SKUs under review?
A.Large items need to be manually reviewed by our team, in order to avoid problems or questions later. The review process typically takes 1 business day. If you find your SKUs under review for more than 1 business day, and you are in a rush to get started, please feel free to contact the Shipwire Care team.
Q.Can I reuse SKUs?
A.Yes, you can reuse SKUs. Shipwire only counts products with 1 or more items in inventory as an active SKU. Products without any inventory the warehouse are only seen for planning purposes.
For example, if you have 200 SKUs in your account, but only 6 of them carry inventory, then Shipwire only sees you as carrying 6 SKUs. Further, if you run out of stock one of the SKUs, and begin carrying stock for another SKU, then Shipwire will still only see you as carrying 6 SKUs.
Q.If I don’t sell items at a master case level why do I need to set up SKUs like this?
A.Shipwire will inventory your items at the level at which you tell us to receive them, as specified in your receiving order.
Storing product in larger case packs will ensure you keep your storage costs to a minimum, while also allowing you to ship out bulk quantities without having to pay for many inventory picks. This is useful in cases of recalls or defective products that need to be sent out in bulk, or for times when you may want to ship back a product or dispose of it. In other cases, such as sending products to trade shows, being able to ship in bulk means saving on handling.
This type of SKU structure also gives our warehouses an understanding of what your item master looks like before your product even gets in. In general, most shipping problems are due to receiving errors, so it helps us prevent issues in the future by better understanding how your product SKUs are set up.
Q.How do I handle sub-characteristics?
A.If your product has variants, such as size or color, then you will need one SKU for each unique item. For example, if you sell a shirt in 3 sizes, then you need one SKU for each size (e.g. 3 SKUs total).
If they also come in 3 colors, you need another 3 SKUs each, bumping it up to a total of 9 SKUs.
If you have cartons that you want to sell wholesale, and you also want to sell the items inside individually direct-to-consumers, then please read our tutorial on master cases for bulk shipping.
Q.Why do I need to enter dimensions?
A.Proper dimensions, weight, and declared value are required to properly use the Shipwire service.
There are a lot of checks and balances in shipping. So if at any time you are found to have submitted erroneous information for a SKU, all shipments associated with that SKU will be rebilled, and the inventory associated with that SKU will be reclassified as Unqualified inventory, typically resulting in additional fees. Please check that all SKUs are properly entered before sending us inventory.
Q.How should I name my SKUs?
A.Most products are clearly labeled with a model number, or other unique identifier. You can name your SKUs however you want to as long as they follow some basic guidelines: they should be clearly and consistently labeled on each item; be no longer than 16 characters; contain no spaces or characters other than a-z or A-Z, or the numbers 0-9.
If you are having trouble finding any unique identifier on your product, consider using the UPC barcode, as long as it is 15 or fewer digits in length. You can use the first 15 letters of the product name, as long as it is listed somewhere on the product.
You can also have your vendor place labels somewhere on each product, with a unique identifier, and use those values.
It is helpful to remember that SKUs typically describe the product, in an extremely brief way. For example, a SKU named TB0003LB12 could be used to describe a t-shirt made by the Think Big Company. The TB stands for “Think Big”; the 0003 stands for the 3rd t-shirt this company made; the L stands for a Large size; and the B12 stands for a bag of 12 “TB0003L” shirts.
Q.How does a mixed order work?
A.If an order contains one Pre-packaged Ready-to-Ship item OR a few Pick ‘n Pack items, shipping is straightforward. You can also have a more complex scenario with an order for 2 or more Pre-packaged Ready-to-Ship items.
Shipwire bills for each tracking number. Since each Pre-packaged Ready-to-Ship item must have its own tracking number, an order for 5 Pre-packaged Ready-to-Ship items would be 5 times the price of a single item to the same address. For example, if you ship 1 Pre-packaged and Ready-to-Ship item, it may cost $5. If you ship 5 of the same item to that same address, the cost would be 5 x $5 = $25.
If an order contains both Pre-packaged Ready-to-Ship and regular Pick ‘n Pack items, Shipwire bills for each tracking number. In this case, there would be one tracking number for each Pre-packaged Ready-to-Ship item, and one tracking number for all the Pick ‘n Packs as a group. For example, if you add 2 Pick ‘n Packs to the previous Pre-packaged Ready-to-Ship order, in a package that ships for $7, your new total would be $25 + $7 = $32.
Q.When and how do I pay for the products I define?
A.You can define as many SKUs in Shipwire as you want, but you will only pay for inventory that is stored in our warehouses.
For example, if you have 200 SKUs in your account, but only 6 carry inventory, then Shipwire only regards you as carrying 6 SKUs. Further, if you stock out of one of the SKUs, and begin carrying stock for another SKU, then Shipwire will still only regard you as carrying 6 SKUs.
Note that if you have a single product stored in several warehouses, then that still counts as a single product and you are only charged for one SKU.